Well I'm all caught up with pictures, except that I did more work tonight, so I'm posting this pics now so I can stay on track! Tonight I decided I was going to install the aileron and flap servos in both wings. I didn't realize at the time what an aggressive goal that was! I work slow and steady, always try to check things twice or three times before I glue or cut, so this step took a while.
checking the aileron and flap deflection:
trial fit control horns and check travel. Seems to be plenty of clearance for both aileron and flap:
after reading the manual completely before starting the build (everyone does this, right?) I discovered that the manual states two different values for desired flap deflection. 70-75% is the max flap deflection based on the latter section of the manual and community knowledge.
1.5" servo arms are installed on the aileron and flap servos in order reach above the surface of the wing from the pocket into which the servos are installed:
I must say that a recent trip to Harbor Freight yielded a great tool which was very handy during this step:
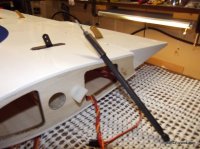
as I mentioned I prefer the socket washer head screws for the servos and other similar applications. The rachet tool proved to be indispensable during this step, as was the hex extension shaft which made it very easy to install the flap servo.
one item to note: the string which is in place to allow the servo wire from the aileron servo to be routed to the wing root was threaded directly through the space where the flap servo is to be installed. It was no big deal to thread the string around the flap servo opening, but it is worth noting. This is something that should be addressed as a build issue for future production runs of the product.
Here is one aileron servo installed and cover attached:
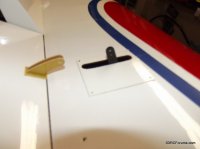
okay a good bit of work, but one wing is done!
fast forward an hour or so....and...
both wings are done, control horns are glued in, and waiting for the epoxy to dry.