Bipenut53
150cc
Hello all!! I am going to build the Light RC 35" Rebel Z foamie airplane here in this log. First off I need to thank 3DRCForums.com, RCFoamies.com, LightRC.com, and [MENTION=2643]3DMIKE[/MENTION] for this opportunity to build this airplane.
The Rebel Z is a Light RC exclusive design, mixing attributes from several classic aircraft. The Rebel Z is a blend of the Acro, Laser, Rebel and variants of these. Using carbon to stiffen the chassis much like an indoor plane would. This stiff airframe allows the plane to fly better, as well as handle more wind, and challenge your 3D skills. This design is the most extreme flying model Light RC is currently offering.
I opened the box and this is the way the airplane comes:
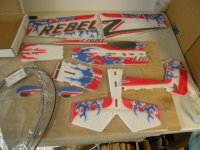
These are the electrics I got with this airplane:
1 Turnigy 3020-1800 brushless motor
4 Li-Power 9g servos
2 Rhino 610 mah 3 cell 20c lipo batteries
1 Guard 20 amp ESC
4 2" servo extensions
I will be adding a mini receiver for Spektrum
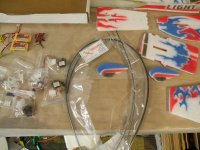
So I will get started and update as I go
The Rebel Z is a Light RC exclusive design, mixing attributes from several classic aircraft. The Rebel Z is a blend of the Acro, Laser, Rebel and variants of these. Using carbon to stiffen the chassis much like an indoor plane would. This stiff airframe allows the plane to fly better, as well as handle more wind, and challenge your 3D skills. This design is the most extreme flying model Light RC is currently offering.
I opened the box and this is the way the airplane comes:
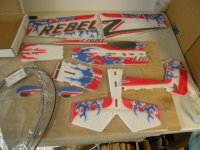
These are the electrics I got with this airplane:
1 Turnigy 3020-1800 brushless motor
4 Li-Power 9g servos
2 Rhino 610 mah 3 cell 20c lipo batteries
1 Guard 20 amp ESC
4 2" servo extensions
I will be adding a mini receiver for Spektrum
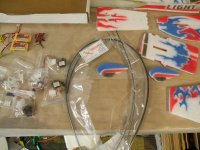
So I will get started and update as I go
Last edited by a moderator: